Fast and Affordable Packaging Machine Repair Services You Can Rely On
Fast and Affordable Packaging Machine Repair Services You Can Rely On
Blog Article
Quick and Reliable Packaging Machine Fixing Services to Reduce Downtime
In the competitive landscape of manufacturing, the efficiency of packaging operations hinges on the reliability of machinery. Quick and trustworthy repair solutions are important in alleviating downtime, which can lead to substantial financial losses and operational troubles.
Relevance of Timely Repairs
Prompt repairs of product packaging devices are essential for maintaining operational efficiency and minimizing downtime. In the busy setting of production and product packaging, even minor malfunctions can result in considerable delays and productivity losses. Resolving issues quickly makes sure that makers operate at their optimal ability, consequently guarding the flow of operations.
Moreover, regular and timely maintenance can prevent the acceleration of minor troubles into major breakdowns, which commonly incur greater fixing expenses and longer downtimes. An aggressive strategy to device repair service not only preserves the stability of the devices but also enhances the overall reliability of the production line.
Furthermore, prompt fixings contribute to the longevity of packaging machinery. Devices that are serviced promptly are less most likely to deal with excessive deterioration, enabling organizations to maximize their investments. This is particularly vital in markets where high-speed product packaging is important, as the need for regular performance is paramount.
Benefits of Reliable Provider
Reputable solution carriers play an essential role in guaranteeing the smooth operation of packaging devices. Their competence not just improves the effectiveness of repair work but likewise contributes dramatically to the longevity of equipment.
Furthermore, a trustworthy company offers detailed assistance, including training and guidance for team on machine procedure and upkeep ideal methods. This not just empowers staff members but also grows a society of safety and security and effectiveness within the company. Overall, the benefits of engaging reputable provider expand beyond immediate fixings, positively impacting the whole operational operations of packaging processes.
Typical Packaging Equipment Problems
In the realm of packaging procedures, different problems can endanger the effectiveness and performance of machines. One prevalent issue is mechanical failing, often coming from wear and tear or inadequate maintenance. Parts such as belts, electric motors, and gears may stop working, resulting in malfunctions that halt manufacturing. An additional typical concern is misalignment, which can cause jams and uneven product packaging, impacting product high quality and i loved this throughput.
Electrical issues can also disrupt packaging operations. Damaged wiring or malfunctioning sensors may result in erratic device habits, creating hold-ups and raised functional costs. Furthermore, software glitches can impede the machine's shows, leading to functional inadequacies.
Irregular item circulation is one more critical concern. This can arise from variants in item shape, size, or weight, which may impact the device's ability to handle things accurately. Ultimately, insufficient training of operators can aggravate these troubles, as untrained workers might not acknowledge early indicators of breakdown or might misuse the tools.
Dealing with these usual product packaging maker concerns immediately is vital to preserving performance and making certain a smooth procedure. Normal inspections and positive maintenance can significantly mitigate these problems, cultivating a reputable packaging environment.
Tips for Reducing Downtime
To reduce downtime in product packaging operations, carrying out a positive upkeep method is essential. Consistently arranged upkeep checks can identify potential problems prior to they escalate, ensuring devices operate effectively. Developing a routine that consists of lubrication, calibration, and examination of crucial components can significantly decrease the frequency of unexpected malfunctions.
Educating team to operate equipment properly and identify very early indication of malfunction can additionally play an essential role. Empowering operators with the knowledge to perform basic troubleshooting can protect against minor concerns from creating major delays. Keeping an efficient inventory of essential spare parts can quicken fixings, as waiting for parts can lead to extensive downtime.
Furthermore, recording equipment performance and upkeep activities can help identify patterns and persistent troubles, permitting for targeted interventions. Integrating advanced monitoring modern technologies can offer real-time information, making it possible for predictive maintenance and decreasing the threat of abrupt failures.
Finally, promoting open communication between operators and maintenance groups makes certain that any kind of irregularities are promptly reported and attended to. By taking these proactive actions, organizations can improve functional performance and considerably reduce downtime in product packaging procedures.
Choosing the Right Repair Work Service
Picking the proper repair work solution for product packaging machines is a critical choice that can substantially impact operational effectiveness. An appropriate company guarantees that your machinery is repaired swiftly, efficiently, and to the highest criteria. Begin by evaluating the provider's experience with your specific kind of packaging tools. A service technician acquainted with your machinery can diagnose problems more precisely and apply options extra swiftly.
Following, take into consideration the provider's reputation. Seeking responses from various other companies within your industry can provide understandings into integrity and quality. Qualifications and collaborations with identified tools makers can also show a commitment to quality.
Furthermore, evaluate their feedback time and availability. A provider that can offer prompt assistance decreases downtime and keeps manufacturing flow stable. It's additionally vital to make inquiries about guarantee and solution guarantees, which can reflect the self-confidence the service provider has in their job.

Final Thought
In her explanation final thought, the importance of dependable and fast product packaging maker repair services can not be overemphasized, as they play a vital role in minimizing downtime and guaranteeing operational effectiveness. Executing proactive maintenance methods and spending in team training more improves the long life of product packaging equipment.
Prompt repair services of packaging devices are essential for keeping functional effectiveness and decreasing downtime.Furthermore, timely repair services contribute to the longevity of product packaging equipment. In general, the benefits of engaging trustworthy solution companies expand past instant repair services, positively impacting the entire functional process of product packaging processes.
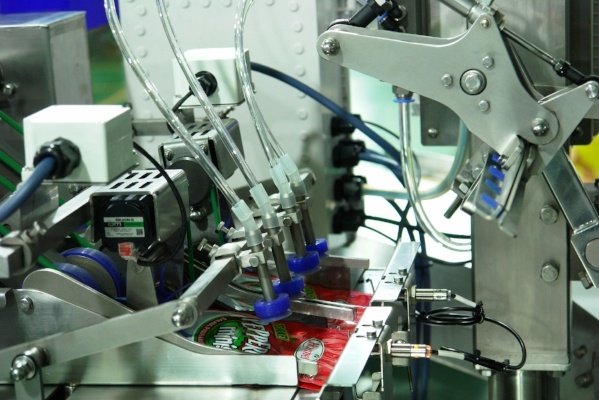
Report this page